Difference between revisions of "The Science of Mashing"
(→How temperature effects enzymatic reactions) |
(→With limited substrate) |
||
Line 89: | Line 89: | ||
If the substrate is limited, the curves for product production over time and temperature optimum will look different. There is a max to the amount of product that can be produced and the temperature and time will determine if the enzymes present will be able to convert all the substrate to reach this maximum. | If the substrate is limited, the curves for product production over time and temperature optimum will look different. There is a max to the amount of product that can be produced and the temperature and time will determine if the enzymes present will be able to convert all the substrate to reach this maximum. | ||
+ | [[Image:Enzyme_product_time_limited.gif|frame|left|Figure X - If the amount of substrate is limted there will also be a maximum for the amount of product that can be created. Now the temperature will determine how quickly this maximum is reached or if the maximum is reached at all. The latter will not be the case if the temperature is to high and too many enzymes are inactivated too early]] | ||
+ | [[Image:Enzyme_temperature_optimum_limited.gif|frame|Figure X - The same is true for the temperature optimum. The longer the reaction time, the broader the temperature range in which the enzymes will be able to convert all the substrate and reach the maximum product concentration]] | ||
All these scenarios also exist in mashing and they will be presented in their respective sections. With alpha amylase and its substrate (starch) we are interested in converting it all. Because of the higher denaturing temperature of this enzymes, there is a wide range of temperatures with which this goal can be achieved. The temperature of a saccharification rest is chosen such that a desired attenuation level is reached. This happens by limiting the beta amylase and this enzyme will not be permitted to convert all is substrate into product (maltose). Last but not least in modern malts the protoelytic activity needs to be limited. That's why not protein rest is held anymore such that the protoelytic enzymes, which are less stable than beta amylase, are quickly denatured and the conversion of their substrate (medium and long chained proteins) is minimized. | All these scenarios also exist in mashing and they will be presented in their respective sections. With alpha amylase and its substrate (starch) we are interested in converting it all. Because of the higher denaturing temperature of this enzymes, there is a wide range of temperatures with which this goal can be achieved. The temperature of a saccharification rest is chosen such that a desired attenuation level is reached. This happens by limiting the beta amylase and this enzyme will not be permitted to convert all is substrate into product (maltose). Last but not least in modern malts the protoelytic activity needs to be limited. That's why not protein rest is held anymore such that the protoelytic enzymes, which are less stable than beta amylase, are quickly denatured and the conversion of their substrate (medium and long chained proteins) is minimized. |
Revision as of 01:36, 5 December 2008
------------- Work in progress ------------
In mashing the milled grain (grist) is mixed with water to create the mash. It is an essential process in the production of beer and a continuation of the malting process on the way to sweet wort. During the mash soluble malt compounds like enzymes, proteins and sugars are dissolved by the mash water and insoluble malt compounds like starch and some long chained proteins are converted into soluble compounds and dissolved into the water. The latter happens through a combination of physical and biochemical process which can be controlled by the brewer to achieve a sweet wort of desired quality. The biochemical processes are catalyzed by various malt enzymes. Their function and behavior is dependent on the conditions in the mash (e.g. temperature, pH, concentration, etc.) and the brewer should be familiar with that behavior in order to control the quality of the sweet wort that is run off from the mash in the lautering process.
Contents
Enzymes
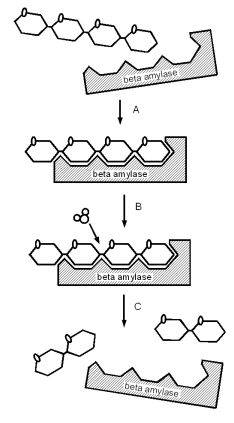
Enzymes are very important to mashing. They catalyze conversion reactions which break down malt compounds (the largest one being starch). In the case of starch this conversion is necessary to form water soluble dextrines and sugars. The latter of which can be metabolized by the yeast. Enzymes are proteins (chains of amino acids) which have the ability to lower the energy needed for a chemical chemical reaction which allows that reaction to occur faster and at lower temperatures. Most enzymes are very specific to the reaction they catalyze and work only with a specific substrate and produce only a specific product. In case of the beta amylase enzyme, for example, the substrate is a glucose chain and the product is maltose. The reaction that is catalyzed the the split of a glucose chain link while a molecule of water is consumed. The highly specific nature to the reaction that is catalyzes stems form the shape of the enzyme which is just right for reacting with the substrate and releasing the product and residual product shortly after. The enzyme itself is not consumed in the reaction. I.e. once free again it can catalyze another reaction.
Without an enzyme a chemical reaction may look like this [rsc.org]:
- substrate1 + substrate2 -> product
But the initial energy (i.e. temperature) needed for this reaction may be so high that it rarely ever happens. With the presence of an enzyme this reaction changes to
- substrate1 + enzyme -> enzyme-substrate-intermediate
- enzyme-substrate-intermediate + substrate2 -> product + enzyme
The energy needed for these enzymatic reactions are now low enough for the reaction to happen at practical temperatures (e.g. mash temperatures).
Here is an eample of an actual enzymatic reaction in the mash. The enzyme is maltase which can split a maltose molecule into two glucose molecules. The reaction consumes one water molecule:
- C12H22O11 + H2O -> 2 C6H12O6
With the enzyme maltase the reaction is actually 2 reactions:
- C12H22O11 + <Maltase> -> C12H22O11-<Maltase>
- C12H22O11-<Maltase> + H2O -> C6H12O6 + <Maltase>
The same is true for other enzymatic reactions in the mash. But for simplicity sake the shorter form of:
- substrate1 + substrate2 -> product
Is also used to show the reaction that is happening. The involvement of the enzyme in this reaction is implied
As mentioned earlier. Enzymes are generally very specific in the type of substrate they work on and which reaction they catalyze. A simple model for that behavior is the lock-and-key hypothesis [rsc.org]. In that theory, the enzyme has a shape that fits only a particular substrate. Like the beta amylase which fits only on the non reducing end of a starch chain (Figure 1). If the shape of the enzyme changes significantly due to temperature or pH or inhibitors block the receptor site of the enzyme it cannot react with the substrate and the enzyme becomes inactive.
Enzyme and substrate concentration

If substrate is available in excess, the reaction activity is proportional to the amount of enzymes. This means that doubling the enzyme concentration will result in twice the product during the same reaction time.
If enzymes are available in excess, the rate of reaction will be proportional to the amount of available substrate. I.e. the more substrate the enzymes have to work on, the faster the product will be created. But as the substrate concentration is increased, the reaction rate will approach a maximum. This maximum is set by the amount of active enzymes. If the substrate amount is further increased the enzyme concentration will become the limiting factor for the reaction.
The rate of many enzymatic reactions follows the following equation (Michaelis-Menten) [wikipedia.org]:
- reaction rate = maximum rate * [S] / (km + [S])
where km is the Michaelis konstant and [S] the concentration of substrate. The Michaelis konstant depends on the type of enzyme and is the substrate concentration at which 1/2 of the maxium reaction rate is reached. The maxium reaction rate depends on the current concentration of active enzymes.
In mashing both effects (enzyme and substrate limitation) exist. In the beginning of the mash, starch is available in excess and the amount of amylase enzymes available (determined by the diastatic power of the malt) determines how fast the mash converts. These effects will be discussed later when the mash enzymes are discussed in detail.
How temperature effects enzymatic reactions
The rate of most chemical reactions, including enzymatic reactions, follows the Arrhenius equation [wikipedia.org]:
- reaction rate = A * e(-ΔG*/RT)
Where A is the Arrhenius constant, a simple non exponential factor for the reaction rate. ΔG* is the activation energy of the reaction and determines at what temperature the reaction will become "significant". R is the universal gas constant and T is the absolute temperature in Kelvin. To convert a temperature in Celsius into Kelvin 273.15 needs to be added to the Celsius value (I.e. the absolute temperature (0 Kelvin) is -273.15 Celsius). But all that doesn't really matter for understanding this subject. What matters is that the reaction rate of an enzymatic reaction follows an exponential curve (Figure 2). For every 10 C (18F) increase the reaction rate increases 1.2 - 2.5 fold [lsbu.ac.uk].
But if the enzymatic reaction rate follows an exponential curve, why are there different temperature optima for different enzymes?
To answer this question we need to look at another effect that temperature has on enzymes. As mentioned earlier, enzymes are proteins (long chains of amino acids) that are shaped in a particular way which allows them to hold onto their substrate during the reaction. This shape is held in place by weak bonds between different amino acids of the chain. But these bonds are easily broken if the temperature gets too high and the enzyme molecule starts to vibrate too much. This doesn't cause the chain of amino acids to get split, these bonds are much stronger and require much higher temperatures, but the enzyme looses its shape and becomes unable to catalyse the reaction it was made for. It is said to have denatured. Above a critical temperature the rate of denature increases 6 - 36 fold for every temperature increase of 10 C [lsbu.ac.uk]. This is much higher than the increase in the reaction rate and as a result, the productivity of the enzyme will decrease is the temperature is raised past the temperature optimum. Figure 3 shows how the enzyme concentration of a hypothetical enzyme drops for 5 different temperatures.
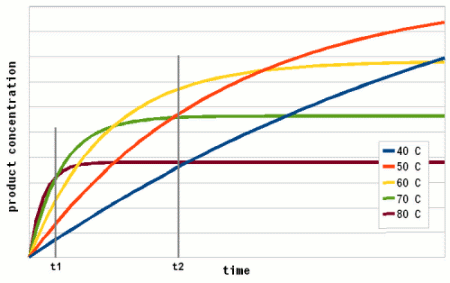
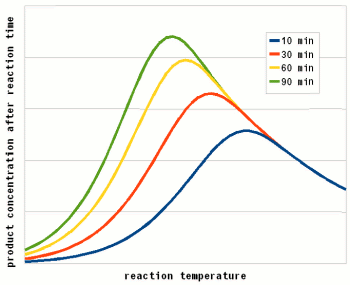
Based one the rate of reaction (Arrhenius equation) and the drop of the active enzyme concentration over time (Figure 3) one can plot the increase of product if unlimited substrate is available. Having unlimited substrate available is not a realistic scenario for mashing but it helps in showing the relationship between the temperature optimum of an enzyme and the reaction time. Figure 4 shows the graphs for the rise in product concentration over time for a hypothetical enzyme at 5 different temperatures. While a high temperature causes a steep initial rise in temperature this high temperature also causes a quick drop in the enzyme concentration and the rise in product concentration quickly levels off and falls behind lower reaction temperatures.
A simple analogy to this behavior is a toy car powered by an electric motor rated for 10V. If the motor is run at 5 volt the car will run very slow but may be able to run for a long time. If run at 10V the car will go faster but only until the motor reached the lifespan it was designed for. Run at 15 V the car will be even faster but the motor is likely to burn out shortly. And if run at 20V the car will get the fastest start of all but won't get far since the motor will burn out quickly. The same happens with the enzymes. At high temperatures they are sprinters and at lower temperatures they are marathon runners.
With limited substrate
If the substrate is limited, the curves for product production over time and temperature optimum will look different. There is a max to the amount of product that can be produced and the temperature and time will determine if the enzymes present will be able to convert all the substrate to reach this maximum.
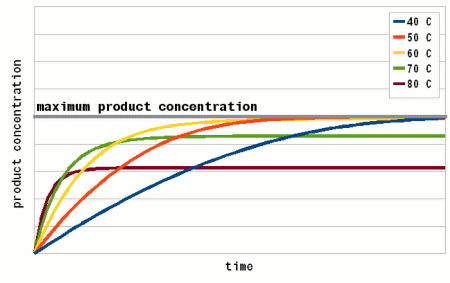
All these scenarios also exist in mashing and they will be presented in their respective sections. With alpha amylase and its substrate (starch) we are interested in converting it all. Because of the higher denaturing temperature of this enzymes, there is a wide range of temperatures with which this goal can be achieved. The temperature of a saccharification rest is chosen such that a desired attenuation level is reached. This happens by limiting the beta amylase and this enzyme will not be permitted to convert all is substrate into product (maltose). Last but not least in modern malts the protoelytic activity needs to be limited. That's why not protein rest is held anymore such that the protoelytic enzymes, which are less stable than beta amylase, are quickly denatured and the conversion of their substrate (medium and long chained proteins) is minimized.
The effect of pH
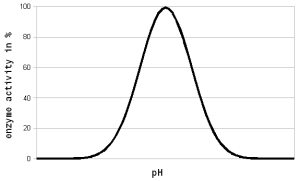
The pH of a solution is a logarithmic measure of the freely available H+ ions. The concentration of these ions affects the enzymes in various ways. A change in pH loads to changes in the charges on the enzyme due to the reaction of the H+ ions with the carboxyl or amino functional groups [cuny.edu].
The at high pH (low concentration of H+ in the solution> the carboxyl group disassociates
- COOH → COO- + H+
This leaves a negative charge at the site of the carboxyl group and donates a proton H+ to the solution. This reaction is reversed at low pH
At low pH (high concentration of H+ in the solution) the amino functional group binds a proton
- NH2 + H+ → NH3+
This results in a positive charge on the site of the amino group. A reaction that is reversed at high pH.
These pH dependent reactions determine the electric charges and as a result the shape of the enzyme and its ability to react with the substrate. As a result a pH exists at which the enzyme will be most efficient performing the reaction it was designed for. On either side of that optimum the effectiveness of the enzyme will decline until it is unable to function anymore.
The change in enzyme activity within 2-3 pH units to either side of the optimum is generally a reversible process [lsbu.ac.uk]. This means that no permanent damage is done to the enzyme. It also means that a suboptimal pH in mashing doesn't necessarily damage the enzymes and that the full enzymatic activity can be restored by adjusting the mash pH into the optimal range, except for the enzymes that have already been denatures. A more severe pH change 3+ units is likely to denature the enzyme due to high stress that the extreme change in the charges place on the structure of the enzyme. This basically makes the enzyme less stable and it denatures at a fairly high rate even below its critical temperature. In some cases strong acidity can also hydrolyze the peptide links (i.e. break the amino acid chain the makes up the enzyme).
When considering pH, it should be noted that the pH of a solution changes with temperature. The rate of change is dependent on the solution itself. For wort and mashes the actual pH is 0.35 units lower at 65 C (150F) than at room temperature 20 C (68 F). At 75 C it is 0.45 units lower [Briggs, 2004].
Inhibitors and cofactors
Some enzymes require the presence of a non protein compound, commonly a metal ion, for the reaction. Without this cofactor the enzyme is not able to catalyze the reaction it was made for. As a result the rate of the enzymatic reaction may also be limited by the concentration and availability of the necessary cofactors. One important cofactor for enzymes needed by the yeast metabolism is for example zink [wikipedia.org]
Inhibitors reduce the reaction rate of the enzymes. Three types of enzyme inhibition exist: competitive, non-competitive and substrate. In competitive inhibition the inhibiting molecule is very similar to the substrate molecule and fits into the active site of the enzyme. But it is not able to complete the enzymatic reaction. As a result the enzyme is blocked. Eventually the inhibitor will free up the enzyme and the enzyme is again able to perform its enzymatic reaction. The higher the inhibitor concentration in comparison to the substrate, the slower the enzymatic reaction [worthington].
In non-competitive inhibition, the inhibitor reacts with the enzyme outside its active site and changes its shape such that the substrate is not able to lock onto the active since and the enzyme is not able to perform its enzymatic reaction [worthington]. This is similar to the change of shape due to pH changes.
In some cases an abundance of substrate can also lead to a reduction in the reaction rate [worthington]. This may be caused by too many substrate molecules competing for a single active site. As a result a given substrate molecule may not stay at the active site long enough for the enzymatic reaction to happen before it is replaced by another substrate molecule.
Starch
- where it is found
- glucose and 1-4/1-6 branches
- amylose
- amylopectin
- starch granule structure
Starch conversion
- gelatinization
- active enzymes
- emzyme temperature and pH optima
- mash parameters affecting conversion
Proteins
Other enzymes in mashing
Sources
Enzymes
- [rsc.org] Chemistry for Biologists - How enzymes work
- [lsbu.ac.uk] The effect of temperature on : [lsbu.ac.uk The effect of pH on enzymes, London Southbank University
- [wikipedia.org] Arrhenius Equation, Wikipedia.org
- [wikipedia.org] Michaelis-Menten kinetics, Wikipedia.org
- [wikipedia.org] Cofactors Wikipedia.org
- [cuny.edu] pH and enzymes, City University of New York
- [worthington] Introduction to Enzymes, Worthington Biochemical